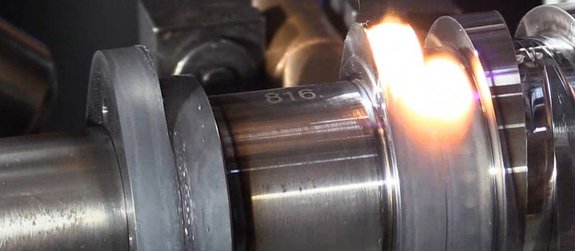
Energy-efficient heat treatment
High-power diode lasers optimize hardening of complex component geometries.
When it comes to surface hardening of steel components, laser systems are said to have a high energy consumption, which is why they have not caught on in every production area. High-power diode lasers, however, can overcome this prejudice since they allow energy-efficient hardening of even complex component geometries, thereby offering an economical, appealing alternative to induction hardening.
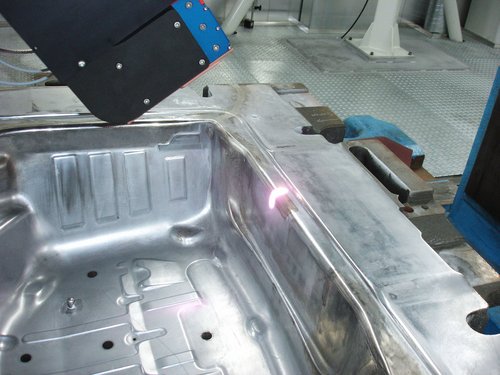
Heat treatment
Heat treatment is a common method for increasing the wear resistance and fatigue resistance of steel components. In this case, a heat source is used to heat up the areas close to the surface of the workpiece to a range of 900 to 1500°C, so much so that the steel structure, which is ferritic at room temperature, changes to austenite.
Afterwards, it is quenched to temperatures below 100°C. During this process, carbon atoms are deposited in a high-temperature lattice structure and cannot diffuse outward because of the quick cool-down: resulting in hard martensite. The laser-beam hardening process is an established approach. Once a niche application, it is being successfully applied today because of its high precision in terms of hardening, and yet the method has not caught on everywhere. In many cases, alternative heat treatment methods, such as induction hardening, are still used. With this application method, the component is usually placed within a copper coil, with an alternating current running through the coil at a certain frequency.
Together, the coil and the component complete an oscillating circuit. This process leads to high frequency remagnetization, which, in turn, leads to the workpiece being heated up. The coupling of the magnetic field significantly depends on the geometry of the component and can potentially take place in areas that usually should not be heated at all, or at least not all that much. With induction hardening, if the local energy inputs are too high, this can lead to undesired material distortion, e.g. of very fine structures, which can only be balanced out by additional post-processing. Furthermore, the components have to be cooled down after heating, either by being buzzed off or being immersed. A water-based quenching medium is normally used for this, but its circulation and cooling requires additional energy.
Why, then, is induction hardening still often preferred despite its high processing effort? The reason can be found in the widespread belief that lasers are uneconomical because of their high energy consumption, while inductive methods are therefore — despite the extra work — the more cost-efficient option. However, this assumption originated from a time when CO2 lasers were the only commercially available high-power sources. With an electrical efficiency of about 10 percent and an optical coupling in steel of a maximum of 40 percent (without the additional absorption-increasing coating), this type of laser does indeed only deliver a low energy efficiency.
Besides, they are expensive to buy. Induction hardening, conversely, reaches efficiencies of between 15 and 63 percent, depending on the component geometry. As a result, the additional effort for post-processing and cooling was estimated to be lower than the investment and operation costs for laser systems. Consequently, it is understandable that many users have preferred inductive hardening over laser hardening to date.
Diode lasers as energy-efficient alternative to induction hardening
But this view does not reflect the current developments of laser technology. In particular, modern high-power diode lasers are clearly superior to the CO2-laser: with an efficiency of 50 percent they have the highest performance efficiency of todays’ laser systems. This has an impact on energy costs. They are also today’s most favorable type of laser when it comes to investment costs. When hardening identical work pieces for example, laser hardening based on diode laser only needs, depending on the application, one-tenth of the energy of an induction process.
One reason for this is the disproportionate high energy consumption at inductive hardening of complex geometries when the less efficient outer coil sections have to be used. Components such as modern cam units — with several closely linked adjacent areas that have to be hardened individually — cannot be treated at all with induction hardening because of their demanding geometry.
Here, laser systems have a clear advantage: the laser beam together with precisely focusable beam shaping optics allow for a selective heat treatment, at which only selected areas of the components are processed. With the combination of optical temperature-monitoring systems such as thermal cameras or pyrometers with quick process controllers, the heat input can be dosed more precisely. Because of this, temperatures that are too low but also local overheating can be avoided.
Compared to inductive hardening, there are further savings. Because of the quick heating, selective processing, and precise temperature control, the heat that is put in per laser beam is dissipated within the shortest time and without additional quenching media into other material layers (self-quenching). So, there is almost no material distortion while post-processing is mainly redundant, which clearly reduces the required time and material. Furthermore, there are no additional energy costs for cooling quenching media because of the self-quenching.
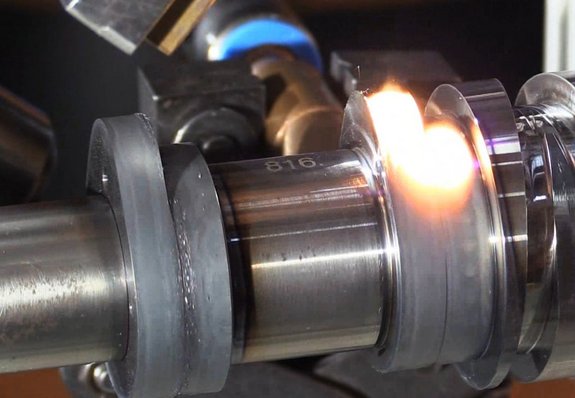
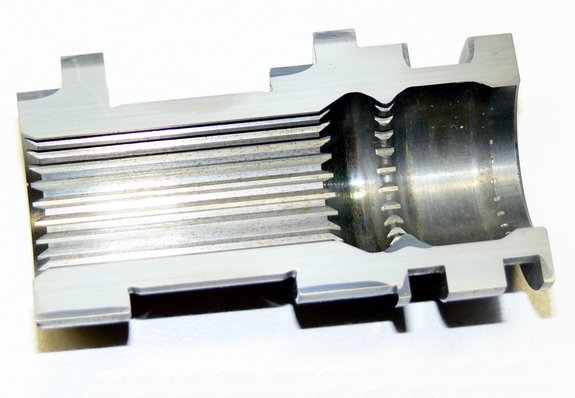
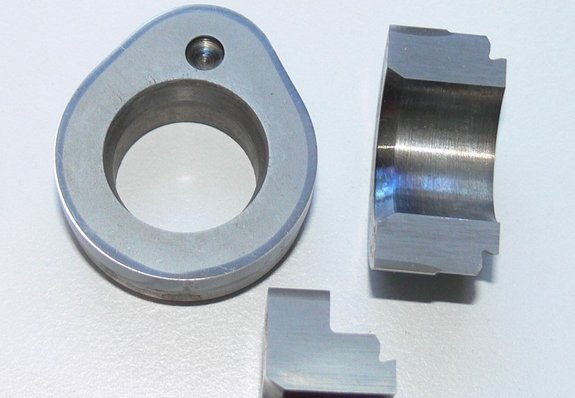
Efficient hardening of steelwork components
Hardening with diode lasers does not only prove itself economically but technologically as well. With diode laser radiation, a nice homogeneous intensity profile can be created. This causes, e.g. at surface treatments, a constant material heating in flat areas. On the other hand, the radiation can be formed statically (with lens systems) or dynamically (with scanners) in such a way that individually adjusted intensity profiles can be realized precisely. As diode lasers are available in the multi-kilowatt range, with this method even large-scale laser spots can be realized with high reliability. Laserline's diode lasers can reach up to 50 kW laser power; maximal flexibility can be reached by using, for example, zoom optics that allow precisely adjustable focus sizes. From camshafts to large-scale forming dies: with this method almost every steelwork component can be hardened with diode lasers.
Conclusion
Is laser hardening not always the better option? Well, the answer is not that simple. A general statement does not make sense here, for it seems better to decide on a case-by-case base: which of the two technologies best fulfills their own requirements, and which one convinces most considering the process results and energy consumption. Who, for example, needs to harden workpieces with a large-scale simple- or cylindrical-shaped geometry is indeed well-advised to go with induction. In this case, this method is the more efficient option. But when workpieces with more ambitious geometrical demands have to be hardened, as in only selected, limited areas, the diode laser-based technology is the more efficient — and sometimes even the only viable — solution. In this case, the diode laser is clearly well ahead as regards energy efficiency.
Read more about heat treatment in our series Diode lasers and their applications - Part 4: Heat Treatment.