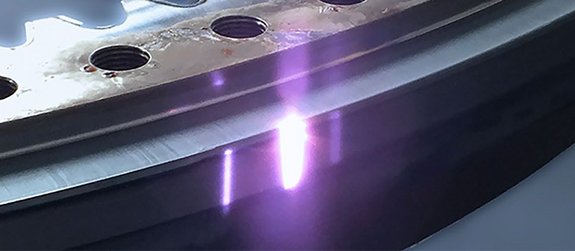
Heat treatment with diode lasers
The heat treatment of metal, such as the hardening of steel, is one of the oldest industrial processes. Its roots go back to antiquity. Even today's laser heat treatments still follow the classical objectives: The targeted application of heat to defined surface areas alters material properties and protects components from wear and corrosion.
Diode lasers and their applications - Part 4: Heat Treatment
Over the last few articles of our little series, we revealed some key areas for the application of diode lasers. Now, we are focusing on a further field of application: heat treatment. Heat treatment is used for hardening machine components, tools, accessory and commodities, but also for softening high-strength materials, too.
Heat treatment of metals
Heat treatment of metal, such as hardening of steel, is one of the oldest industrial processes, with its roots stretching back to antiquity. Even modern-day laser heat treatments still share these traditional objectives: the targeted application of heat to defined surface areas alters the material’s properties and protects components from wear and corrosion.
Component hardening
Diode lasers are especially suitable for hardening the surface of steelwork components. The laser beam heats up areas close to the surface of a workpiece to between 900°C and 1500°C, causing the heat-induced austenitization of the originally ferritic-perlitic steel structure. When the beam moves on, the material on the processed part cools down quickly (self-quenching), creating hard martensite. For many reasons, this process can clearly be realized more efficiently with lasers than with induction coils or gas flames. Firstly, the material physically heats up more quickly than with other methods. Secondly, the zones of relevance for hardening can be treated more selectively, meaning that the local heat input only heats up certain parts of the workpiece. And thirdly, the heat input can be dosed in an exact manner by means of special beam shaping optics with integrated pyrometers or thermal cameras, not least with particular focus on different local heat conductions for the same component. Thanks to these characteristics, the diode laser is extremely well-suited to treating geometric complex structures that require hardening in some zones but have to keep their ductility in others. Furthermore, these process advantages allow for cost savings. That is, because of the low deformation and self-quenching of the material, usually no (or only little) action is required in terms of distortion compensation and cooling. Finally, this has a positive impact in terms of the time and material required.
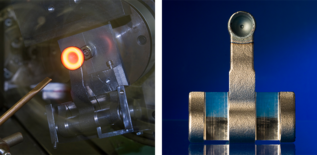
Where are diode lasers used for hardening?
This treatment is especially ideal for wear-stressed or cyclically stressed components such as camshafts. In every gasoline and diesel engine, steel rubs against steel. As a result, the contact zones need to be hardened, otherwise the parts are unlikely to have much longevity. The inductive method is of little help when it comes to these complex structures. The construction of modern camshafts (with different shaped cams and shifting gates for the cylinder deactivation or change in the engine control) requires precise surface hardening which is only possible with diode lasers. Diode lasers have even been long-established in the manufacturing of large sheet metal tools, with the oldest hardening systems in this regard already having been in use for 10 to 15 years. As the prices of laser beam sources have been decreasing for years now, new applications are continuously being explored alongside these typical fields of use.
Softening materials
Heat treatment with diode lasers does not only enable the material to be hardened: it also does the exact opposite, namely, softening the material. Here, the solidified structure is softened in certain zones by heat exposure (“tempered”) or is, for instance, turned back into a ferrite-pearlite structure by austenitization followed by slow cooling. The result is a sheet that is easier to shape or weld. Here, the diode laser is a better tool than other methods, such as induction, gas flames or infrared rays. On the one hand, material processing can be carried out in a highly flexible and precise manner, just like with hardening; on the other hand, the transition zone created between the processed and unprocessed raw material is smaller than that created with other technologies. However, diode lasers have a very homogeneous intensity distribution, even for big spots, which makes the results of the softening especially even.
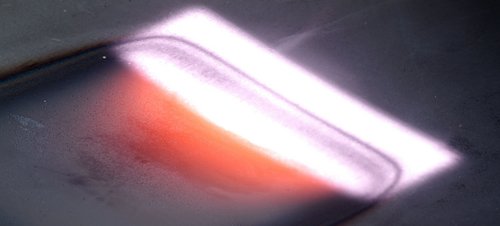
Where is softening used?
Softening can actually save lives: in car body construction, soft deformation zones can be created at press-hardened areas, these zones absorb impact of energy in the event of crashes and thereby protect the body. This flexible material processing ensures that the total stiffness of the steel is maintained in the remaining zones. A further field of application is deep drawing, which sees the circuit board be softened in the intended bending zones before pressing to avoid cracks or fractures during the forming process.
Incidentally, diode lasers can also be used for drying printing inks. As part of this process of “setting”, the ink layers are heated with a laser beam, and because of temperature-induced increased viscosity, they are more quickly absorbed by the printing material. The modular, compact components of the laser can be directly integrated into the systems of offset printers.
Conclusion
This clearly demonstrates why heat treatment is one of the main fields of application for diode lasers — compared to other methods, they are simply streets ahead. Thanks to their targeted heating, the lasers are more flexible, more precise, and even more economical than induction, gas flames, or infrared radiators. And that’s not all: the universal tool of the diode laser can also be used for brazing, which our next blog article will explain further.
Until then, those seeking to immerse themselves in extra information about this topic will find them at Applications Heat Treatment.