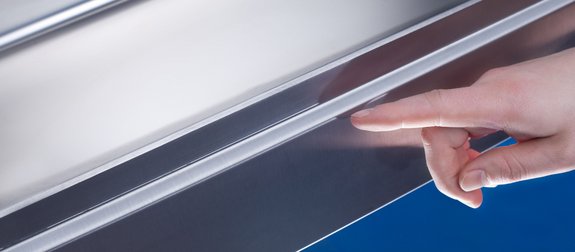
Diode lasers and metal welding
The application fields of diode lasers are are broad and diverse – but there are certain key areas. One of them is the process of metal welding.
Part 2: The welding process
At the start of our short series, we clarified what exactly a diode laser is, and today we are looking at its fields of application. As previously mentioned, these fields are broad and diverse, even though there are certain key areas in which diode lasers are very much at the forefront. One of them is the process of metal welding. Diode lasers play a decisive role in various industrial areas: from the wafer-thin copper electric contact-sheet to centimeter-thick ships’ sides made from steel, countless metal components are joined by welding. Today, diode lasers cover the entire joining spectrum and offer suitable tools for a plethora of welding applications. Compared to traditional arc welding methods like MIG/MAG or WIG welding, as well as other laser-based welding techniques, welding with diode lasers is often superior.
Benefits
In fact, diode lasers are actually ideal for industrial welding processes. There are several reasons for this. Firstly, the combination of high power output and comfortable spot sizes allows for optimum gap bridgeability. Secondly, the energetic homogeneity of the spot and the high absorption capacity of a typical wavelength mix generate unusual calm melt pools that leave almost no impurities on the areas adjoining the seams through spatters or wavelets. This guarantees excellent seam qualities. Thirdly, diode lasers provide the highest energy efficiency of any industrial laser, which, along with their low maintenance costs, also makes them perfect for welding in series production. Fourthly, these lasers can be used for heat conduction welding as well as keyhole welding applications.
Keyhole welding is a typical laser welding method for components with medium to substantial material thicknesses. The joining partners are irradiated with high intensity to create a vapor capillary in the direction of the beam – a tube-like shape with a hollow filled with metal vapor (keyhole). This enables the deeper layers of the material to be molten; the depth of the melt zone is usually greater than its width. The inner walls of the vapor capillary also reflect the laser beam so that the absorption of the yielded energy is strengthened, thereby causing a sizable melting volume. Highly stable connections are created between the joining partners that withstand even the most demanding stress. Typical applications are, for example, the joining of tailored blanks in automotive assembly or thick-sheet welding. As combined diode laser systems can reach powers of up to 60 kW today, even ships’ sides of 50 mm thickness, massive steel braces in foundations, or offshore wind turbines can all be welded with only two welding runs (layer and opposite side).
If workpieces of a low material thickness have to be joined, keyhole welding is no longer automatically suitable. The high energy input could cause material separations instead of joining, and would certainly lead to major deformations. As a result, heat conduction welding is almost always used in these cases. With its welding penetration depth of a maximum of 2 to 3 millimeters, the method is also suitable for thin sheets or metal foils. The diode laser fuses the joining partners along the planned seam; the melts merge and then solidify towards the desired weld seam. The material barely distorts, while the joining is exceptionally simple and clearly quicker than WIG welding, for example. Thanks to the homogeneous, even heat exposure of the diode laser, the seams are smooth and non-porous, rarely needing post-processing. This high seam quality makes the method especially ideal for visible areas, as, for example, in the joining of metal sinks. Besides, it has also proven itself in fields outside the sphere of design, such as in geometrically highly demanding components including gaiters for pipes.
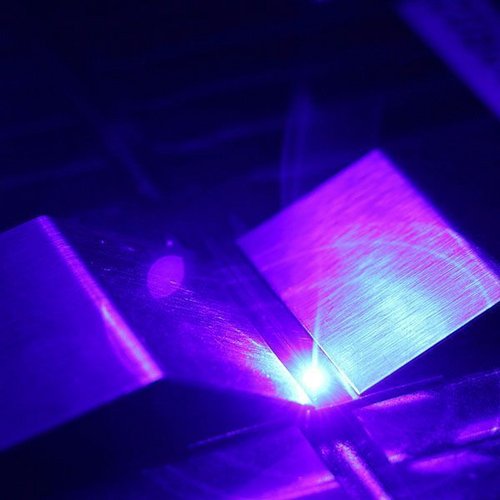
With the development of the LDMblue with 450 nm and, by extension, the blue light wavelength, the world’s first high-power diode laser is even now available, allowing for the controlled spatter-free heat conduction welding of very thin non-ferrous components made from copper or precious metals such as gold. For these materials, heat conduction welding with the traditional infrared lasers is not a feasible option as the infrared radiation is strongly reflected by non-ferrous metals, meaning that the surface can only be molten with a high-intensity beam. However, blue laser light is very well-absorbed by non-ferrous metals, with the result that the workpieces can be molten with substantially lower energy input as well. In this, even wafer-thin electrical contacts made from copper, e.g. those used in electromobility, can be reliably joined. Here, as well, very smooth and visually pleasing seams are created that are also a winning option thanks to their excellent electrical conductivity, offering a new, innovative procedure, with the corresponding high levels of precision, to industry 4.0 and its high-tech requirements.
As you can see, the diode laser is a real universal tool for metal welding, and is truly without compare. And because work is continuing on optimizing the relationship between laser power and beam quality for every type of diode lasers, the range of fields of application for laser welding will likely grow further.
That is it for now. More detailed information on the use of diode lasers in welding can be found in the applications section under laser welding. Our next input in this series will focus on a related topic: cladding with diode lasers. We look forward to hosting you!