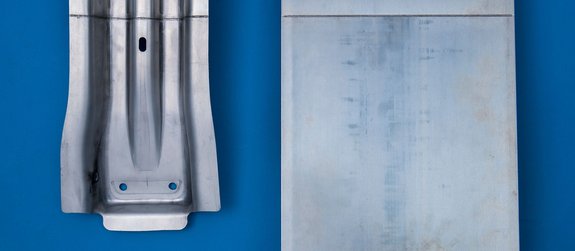
Arcelor Mittal Tailored Blanks counts on Laserline's diode lasers
Fiber lasers – initially, this seemed to have been the first choice. Arcelor Mittal Tailored Blanks (AMTB) wanted to replace their old CO2 lasers and had already identified a favorite. However, Laserline took out the race. Surprised? Only if you don’t know the technology.
Why 30 percent when you can have 50?
Producers of shaped plates like Arcelor Mittal Tailored Blanks (AMTB) need their lasers for welding – and they weld a lot. Until the single sheets of the tailored blanks are put together, some seams must be set — around the clock, 365 days in the year. So, energy efficiency plays an important role. Here, CO2 lasers are unfortunately not much fun for the user: with an efficiency rate of just 10 percent, they cannot make an economical process control possible under today’s production conditions. When about 90 percent of the energy is lost, the continuously increasing electricity prices can really hurt, especially when the created heat loss can only be coped with a cooling system. And it doesn’t even help that CO2 lasers have proven themselves qualitatively and have always been providing good welding results.
No wonder that users of CO2 lasers are looking for alternatives. But which technology should they count on? The aforementioned fiber lasers guarantee excellent welding results. This is known and also proven in tests of AMTB. However, usage of these lasers is only compatible in a limited way with the goal of maximizing energy efficiency. Certainly, the efficiency rate of fiber lasers is higher than that of CO2 lasers. But at about 20 percent, what they achieve is still unsatisfactory as 70 percent of the energy is still lost and must be dissipated as heat. Of course, this exclusively pleases the electricity suppliers.
However, you have to be fair: efficiency rates of 70, 90 percent or more, as some technologies claim, are not realistic for the industrial area. If you take a look at the history of laser, 30 percent of the fiber lasers set the bar quite high. Nevertheless, this does not mean that all possibilities have already been exhausted. In the end, it was logical for AMTB to opt for Laserline’s diode lasers. Because these diode lasers do have an advantage that makes them unique: they transfer electricity without detour over a pump medium into light and thus reach efficiency rates of almost 50 percent. Compared to CO2 or fiber lasers, this is a quantum leap. Why? Because it makes a big difference if in the end, a tenth, a third or at least half of the invested energy is transformed into laser light while the cooling efforts are appropriately reduced. On a yearly basis, the operation costs are clearly reduced.
But it was not only a matter of energy efficiency; the welding results were also fairly convincing. Metal splashes on metal plate and laser optics? With Laserline’s diode lasers, those impurities became rare even though the working distance between plate and laser was not very big. But the calm molten pool was not the only surprise: even the welding seams were smoother and cleaner than those of CO2 or fiber lasers. What more could you want! Maybe bridging bigger gap distances? Here, diode lasers could also score, as their beam diameter is bigger than that of the competition. And the catalog values “protection class IP 54” were also confirmed in practice. Metal dust and splashing water cannot harm the lasers, as the addition of compressed air prevents any intrusion. Protective housings thus become redundant, thereby saving money.
Highly efficient, powerful and robust even under rough process conditions, Laserline’s diode lasers have turned out to be the ideal solution. Consequently, they could prove themselves also in mass production. And there, they can immediately impress: several AMTB production plants in Europe, India and Australia have in the meanwhile shifted to Laserline’s diode lasers. Quality speaks for itself.