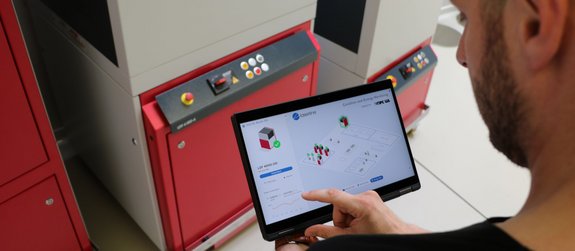
Lasers Meet Digitalization - Industry 4.0
OPC UA interfaces create a basis for platform-independent, vertical and horizontal data communication. They support the integration of lasers, optical fibers and processing optics in smart factory system architectures.
The trend towards digitalization has long since reached the field of industry lasers as well. Laserline reacted early and has engaged itself under the watchword ‘Digital Laser Solutions’ with the development of solutions for the integration of lasers into digital process architectures. First step: The equipment of the LDF systems with an Industrie 4.0 compliant OPC UA interface.
Without any shadow of a doubt, lasers 4.0 will dominate the future because the digital transformation will not stop at laser technology. And why would it stop there? When the Smart Factory will be realized in the future whereby all process participants are linked with each other, just as machines and devices, administration and control units intensively communicate with each other, then diode lasers should be involved, too. The digitalization of a fully automated production street, for example, should also be carried out with lasers. And even there, where digitalization does not mean complete interconnection such as in smaller medium-sized companies, there is no getting around the digital transformation process. A contract coater does not need to integrate dozens of laser systems into a fully automated architecture, for to build up such structures is not always reasonable. However, the contract coater will most probably still want to control and monitor his lasers digitally. The reason is the same as in the large industry: because digitalization promises more efficient and quicker processes that contribute to a reduction of operation and investment costs and to allow for a more effective, concentrated and pleasant operation. Industrie 4.0 will therefore be used extensively, whether in the long or short run.
Industry 4.0 - Platform independent communication via OPC UA
Producers of industry lasers have had to adapt themselves to this change, otherwise the future will belong to others. Laserline realized this at an early stage and has started under the watchword ‘Digital Laser Solutions’ with the development of Industrie 4.0 solutions for its diode lasers. And the first results are already in: All Laserline LDF diode laser systems of the latest generation are with immediate effect also available with OPC UA interfaces. That means, they master the widespread communication standard Open Platform Communications Unified Architecture, which allows for a platform-independent data exchange between most machines, devices and control systems. Thus, LDF diode laser systems can, by means of corresponding interfaces, be integrated into all Industrie 4.0 process architectures on an OPC UA basis, which for the huge production streets in the automotive industry and their suppliers has inter alia an elementary meaning. And it gets even better: Laserline also offers this solution as retrofit for existing LDF systems. All already delivered LDF systems of the 5th and 6th generation can retrospectively be equipped with OPC UA interfaces and can thus be prepared for the Industrie 4.0 integration. In this case, the interfaces are installed as additional hardware components and are coupled with the control unit of the laser system, while in the version ex works, they are already integrated as a software component in the control unit.
Looking forward, the Digital Laser Solutions concept will of course not be limited to LDF lasers. Rather, this approach will be extended to the highly compact 19" diode lasers of the LDM series. Revolutionary systems like the blue diode lasers of the LDMblue series will be available as industry 4.0 compatible versions. In addition, Laserline is working on simple handling applications that allow convenient digital monitoring and control even for stand-alone laser installations.
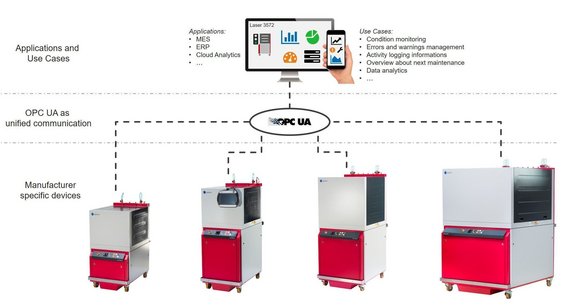
Smart Factory: Access to machine data in host SCADA or MES systems
But what exactly are the benefits of the OPC UA ability of the laser systems for the user, and how will its potential be activated? With the implementation of the OPC UA interface, the laser systems can be integrated into the comprehensive Industrie 4.0 communications. By providing a detailed data pool, they form the basis for data follow-up processes in a production environment. Both quantitatively and qualitatively adequate databases are the precondition for all innovative analyses and evaluations.
In general, every OPC UA interface needs an OPC UA client as counterpart. In Industrie 4.0 architectures, this client is usually integrated into a host SCADA or MES system or into a cloud solution where it is in a manner of speaking the key to the interface lock. What does the client unlock? In the case of diode lasers, nothing but machine data. However, there are many: In the case of LDF systems equipped with the OPC UA system ex works, the user can read out depending on the laser configuration more than 300 values, with retrofit systems still 150. This means that almost everything you want to know about the laser gets collected: What is the current and maximal output power? How is the temperature developing in the system? Is the cooling water flowing alright? Could humidity have come into the system that requires a temporary shutdown of the laser? What is the serial number of the target system and how many of its intended operating hours have already passed?
Machine data
These and similar questions are answered by the machine data very precisely. Additionally, there are automated warnings and error messages that call attention to critical developments. The user can optionally monitor the system and can include all system conditions in the process planning. This reduces the risk of process mistakes and prevents some unpleasant surprises. Superior to conventional data analyses and diagnoses, the delivery of data via OPC UA is also the basis for trendsetting analyses based on approaches using artificial intelligence.
Special advantages in system service: Condition Based Maintenance
Special advantages offer data access and thus attain transparency in the maintenance field. In the past, periodical maintenance services were carried out here, similar to the motor vehicle section by referring to the system age or operating hours. This inflexible approach was not always optimal, because every application stresses the system differently and mistakes can appear away from the maintenance dates. With the comprehensive machine data that can be read out with the OPC UA interface, the user can handle a far more flexible and practical maintenance course. As all relevant data are available, a predictive or condition-based maintenance can be realized in the future. The laser is only maintained when its current condition requires it, or even better: it is already maintained when it can be foreseen that a critical condition could be attained. So, you do not wait until it is getting hairy, but you intervene at an early stage. With this approach, downtimes can be minimized and can additionally be taken into account betimes so that possible replacement systems can come into action. If an unexpected mistake still occurs, it can be sorted out far more quickly than hitherto thanks to the great data pool which is also an important process advantage.
The actual maintenance process can be optimized by this approach as well. When the service provider is interlinked with the applicant, the data read-out allows for an automated service coordination: as soon as maintenance action appears, the responsible service technicians will get an automated indication. In a complete interconnected Smart Factory, this process can even lead to an automated appointment allocation. In any case, it allows for a fairly smooth coordination.
And when the laser has reached the end of its life cycle? This can also be seen from the data, and here the OPC UA interfaces have certain benefits, because according to the warning message it will reach the user in time. The user then has to react and obtain a replacement because this is something that the interface cannot carry out. However, the user cannot claim that s/he did not know anything about this.
Interview with Dr. Alexander Arndt, Manager Digitalization and Process Design
Oh, by the way, LDF diode lasers with OPC UA interfaces are currently being used successfully in the industrial environment as a basis for customer-specific analyses. This shows clearly that the chosen path is the right one. As already said at the beginning, lasers 4.0 will inherit the future.
Questions on OPC UA or the integration of our laser systems into Smart Factory system architectures?
Please do not hesitate to contact us!
Contact