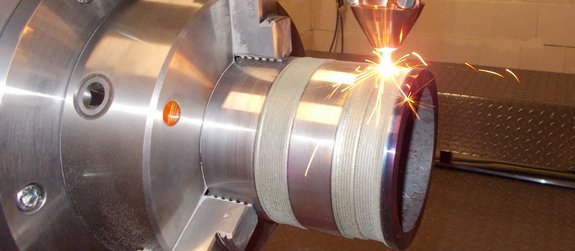
Membrane wall cladding with thermal laser spraying
Up till now, anti-corrosion coatings of membrane walls represent a formidable challenge. Convincing results have disadvantages like big layer thicknesses and heavy deformations. Thermal laser spraying with the use of Laserline’s diode lasers demonstrates that there is an alternative.
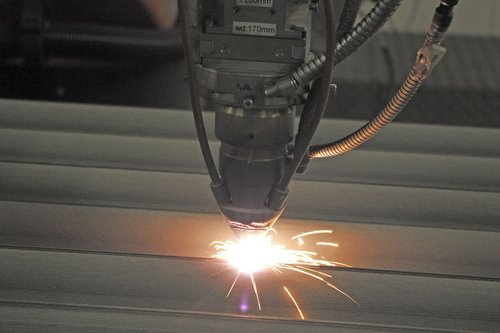
Chlorine attacks metal, a fact that is known all too well by operators of biomass facilities and incineration plants. But why? The boiler walls of such plants consist of water-bearing steel pipe systems that absorb the thermal energy of the firing and then transfer it to the water-steam circuits. But the chlorine in the flue gas of the firing breaks down the pipes. Untreated, they are often no longer usable after one year. It seems reasonable then to assume that this cannot be economical.

Meanwhile, many plant operators therefore count on anti-corrosion coatings. This is already worth the effort as soon as the duration of the operation is doubled — and even more can be achieved: compared to uncoated pipes, and depending on the applied material and physico-chemical load, a tripling or quadrupling of the lifespan is possible.
However, a coating becomes difficult when membrane or finned walls are installed in the boiler. At this type of pipes, the boiler pipes are connected with each other by means of metal bars — the so-called “fins”. These bars create a closed wall surface, which optimizes the heat absorption. Due to this, the surface geometry becomes more complex and pushes many traditional coating technologies to their limits. In particular, the transition from the bent boiler pipe to the straight fin makes most applications fail. In the past, only the classical laser cladding could be used expediently. It even masters critical surface geometries and creates stable layers that are connected metallurgically with the base material.
But no matter how successful the classical laser cladding has been, two major drawbacks ought to be accepted. On the one hand, the coatings were not as corrosion-resistant as required, because the layer and base material strongly intermixed when welded. To compensate for this, bigger minimum thicknesses were used. On the other hand, the higher heat input caused material deformations that made cost-intensive post-processing necessary.
These disadvantages bothered the coating expert Häuser & Co. GmbH. Based on a self-developed plasma spraying technology with downstream heat treatment, their inventors from Duisburg developed a new method that uses the Laserline LDF 6000-100 diode lasers and combines the processes of the thermal spraying and laser cladding: thermal laser spraying. With this coating technology, the diode laser melts — in a way similar to cladding — the coating material in powder form with the surface of the workpiece and thus creates a metallurgical connection. As the even energy distribution within the diode laser beam creates a calm molten pool and an optimized penetration depth, the layer and base material only mix a little so that the layers are far more corrosion-resistant than coatings that are welded in the traditional manner. Also, the complex surface structures and especially the critical transition areas between the pipe and fin do not pose a problem anymore. As the laser beam can be regulated finely within milliseconds and can be directed to the workpiece from changing directions, it exactly customizes to all surface structures when melting. Thus, deformations occur only very rarely. The final results are homogeneous, almost non-porous protective layers. They can be realized in short process periods and mostly need no post-processing.
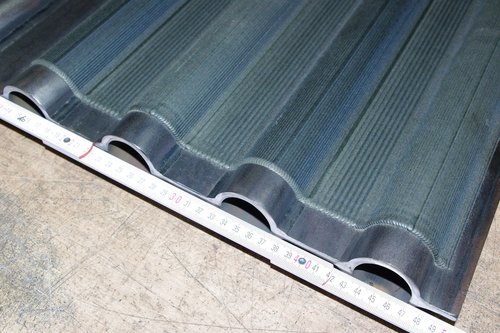
Conclusion:
Thermal laser spraying works in a more material-friendly manner than already existing technologies; it is also more precise and renders a more economical process control possible. Known and proven coating materials like Inconel 625, Hastelloy C or Stellite 21 can also be used here without restrictions. Furthermore, the technology is also suitable for other coating applications such as the coating of industrial valves and drive shafts, repairing used sealing plates, spindles and roll necks, and last but not least for use in the maritime sector.