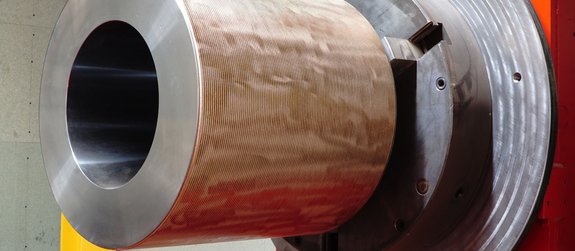
Laserauftragschweißen heute: Wo steht die Technik? (Teil II)
Maschinenmesser und Kesselwände, Bremsscheiben und Getriebelager: Das Spektrum der Bauteile, die mit Diodenlasern beschichtet werden, ist breit gefächert. Entsprechend vielfältig gestalten sich heute auch die bestehenden Beschichtungsverfahren. Teil 2 unserer Serie zum Laserauftragschweißen gibt einen kleinen Überblick – ohne Anspruch auf Vollständigkeit, versteht sich.
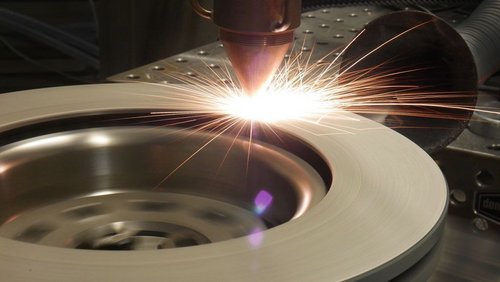
Beschichten, Reparieren, Generieren
Im Dreiklang des Laserauftragschweißens – Beschichten, Reparieren, Generieren – ist das Beschichten gewissermaßen der Grundton. Es wird vor allem zum Schutz neuer Bauteile eingesetzt und soll deren Lebensdauer verlängern. Karosserie- und Getriebekomponenten, Öl- und Gaskessel, aber auch Rohrwände in Kraftwerksanlagen werden beispielsweise durch Antikorrosionsbeschichtungen vor Rost, aggressiven chemischen Verbindungen oder gefährlich hohen Temperaturen geschützt. Bei Maschinenmessern, Achsen, Wellen oder Bremsscheiben, die im täglichen Einsatz starken Stoß- und Reibkräften ausgesetzt sind, erhöhen spezielle Verschleißschutzbeschichtungen die Standzeit. In Getriebelagern können Gleitbeschichtungen kritische Materialreibungen in An- und Auslaufphasen verhindern, wie etwa in den Gleitlagern von Windkraftanlagen. Bei Landmaschinenmessern kommen zudem auch Spezialbeschichtungen vor, die für Selbstschärfungseffekte im Feldeinsatz sorgen.
Bei all diesen Anwendungen hat sich mittlerweile der Diodenlaser als effektivstes Beschichtungswerkzeug durchgesetzt und dabei auch konkurrierende Technologien wie Thermisches Spritzen oder Plasmaauftragschweißen verdrängt. Mit seiner Hilfe lassen sich alle klassischen Beschichtungsmaterialien wie etwa Wolframcarbide exzellent verarbeiten und qualitativ hochwertige Schichten unterschiedlichster Dicke realisieren.
Der Erfolg des Beschichtens mit Diodenlasern beruht nun allerdings nicht allein auf den generellen Vorteilen dieses Lasertyps, die im ersten Teil unserer Serie beschrieben wurden. Mindestens ebenso wichtig sind die verschiedenen Prozesse, die Hersteller wie Laserline in Zusammenarbeit mit ihren Technologiepartnern entwickelt haben, um den unterschiedlichen Bauteilen und deren Einsatzprofilen gerecht zu werden. Beschichten ist hier nicht gleich Beschichten, und was für Karosseriebleche perfekt ist, kann bei Messern, Bremsscheiben oder Zahnrädern der falsche Ansatz sein. Die Beschichtungsverfahren sind denn auch so vielfältig wie die Bauteile selbst. Gleichwohl lassen sich gewisse Grundzüge definieren, die sich bei vergleichbaren Bauteilen wiederholen.
Am unkompliziertesten gestaltet sich zumeist die Beschichtung planer Bauteile. Klassische Metallbleche lassen sich üblicherweise in mehreren Bahnen mit dem Breitstrahl überfahren und so schnell und effektiv beschichten. Für Großbauteile wurden spezielle High-Volume-Verfahren entwickelt, bei denen Diodenlaser ihre Leistungsvorteile voll ausspielen können. Mit 11 bis 20 kW Laserleistung und rund 90 Prozent Pulverwirkungsgrad werden hier bislang unerreichte Pulverauftragsraten von bis zu 14 kg/h erzielt. In Tests mit 50 kW Laserleistung wurden sogar schon Pulveraufträge von circa 35 kg/h und Flächenraten von rund 3,5 m²/h erreicht – verglichen mit Standardverfahren eine Verdreifachung der Beschichtungsleistung.
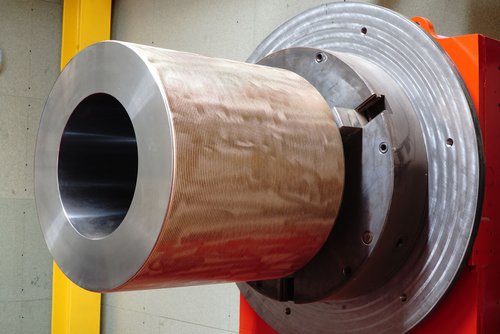
Einsatz von Rundspots
Schon bei planen Bauteilen mit schwankender Dicke gestaltet sich die Umsetzung aber nicht mehr ganz so einfach. Bei Maschinenmessern etwa, die sich Richtung Klinge verjüngen, würde eine Breitstrahlbehandlung verhindern, dass die eingebrachte Wärme in angrenzende Bauteilbereiche abgeführt werden kann. Das Ergebnis wären Verformungen oder sogar Abschmelzungen im Klingenbereich. Um solche Beschädigungen zu vermeiden, müssen deshalb punktgenauere, energetisch wohldosierte Bestrahlungen mit dem klassischen Rundspot realisiert werden, die genau auf das jeweilige Bauteildesign zugeschnitten sind. Dasselbe gilt bei Bauteilen mit komplexen Oberflächengeometrien wie etwa Gleitlagern oder Zahnrädern. Mit dem Breitstrahl kann auch hier nicht effektiv agiert werden. In Frage kommt deshalb nur eine punktgenaue, individualisierte Beschichtung unter Einsatz von Rundspots.
Auch bei rotationssymmetrischen Bauteilen wie Getriebeachsen oder Metallrohren ist das schnelle Überfahren problematisch, da eine Bearbeitungsoptik mit Beschichtungsdüse nicht vollständig um ein Werkstück rotieren kann. Zwar wäre eine Rotation der Optik grundsätzlich denkbar, die Gravitationskräfte würden jedoch einen gleichmäßigen Pulverauftrag unmöglich machen. Als Alternative wurden deshalb spezielle High-Speed-Varianten entwickelt. Die Prozessoptik ist hier fixiert, und das Bauteil wird auf einer Drehbank in vertikaler Richtung um seine Längsachse bewegt, bei durchweg sehr hohen Drehzahlen. Mit diesem Ansatz lassen sich unter geringem Zeitaufwand hohe Flächenraten erzielen, und durch die kurze Einwirkzeit des Lasers sind sehr dünne Beschichtungen möglich. Derselbe Lösungsansatz wird bei Verschleißschutzbeschichtungen für Bremsscheiben genutzt, nur dass hier eine horizontale Drehrichtung realisiert wird.
Fazit
Wie vielfältig das Beschichten mit Diodenlasern ist und welche Möglichkeiten es bietet, lässt sich anhand dieser Beispiele natürlich nur teilweise erfassen. Eine erschöpfende Darstellung würde Bücher füllen. Gleichwohl machen schon diese kleinen Ausschnitte deutlich, warum Diodenlaser aus dem industriellen Beschichten nicht mehr wegzudenken sind: Sie haben sich schlicht als Universalwerkzeug erwiesen. Nicht zufällig wurden deshalb auch bereits neue Anwendungen ins Visier genommen, wie zum Beispiel Kupferbeschichtungen, die sich mit blauen Diodenlasern sehr energie- und materialeffizient realisieren lassen. Doch ehe wir davon berichten, setzen wir zunächst unsere aktuelle Serie über das Laserauftragschweißen fort. Der nächste Teil widmet sich in Kürze dem Reparaturschweißen – bleiben Sie dran!
Erfahren Sie mehr über das Laser Cladding.