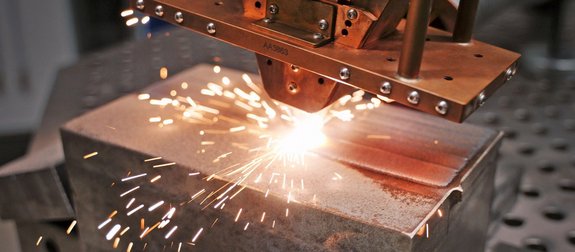
Laserauftragschweißen heute: Wo steht die Technik? (Teil I)
Beschichten, Reparieren, Generieren – all diese industrietypischen Bearbeitungsmethoden lassen sich mit ein und demselben Verfahren bewältigen: dem Laserauftragschweißen. Das flexible Beschichtungsverfahren ist ein regelrechtes Multitalent, überzeugt es doch in allen drei Anwendungsgebieten durch hervorragende Ergebnisse.
Teil 1: Grundlagen des Laserauftragschweißens
Nicht umsonst wird es heute auf breiter Ebene erfolgreich eingesetzt – vom Automobilbau über die Schwerindustrie bis hin zur Landtechnik – und verdrängt dort zunehmend herkömmliche Technologien. Und hier ist noch längst nicht Schluss: Denn durch technologische Weiterentwicklungen kann das vergleichsweise junge Verfahren immer neue Einsatzbereiche erobern. Egal, ob Fachmann oder Laie: Ein Blick auf den aktuellen Stand der Technik lohnt sich also. Grund genug das Verfahren im Rahmen unserer vierteiligen Serie „Laserauftragschweißen heute: Wo steht die Technik?“ einmal genauer zu beleuchten.
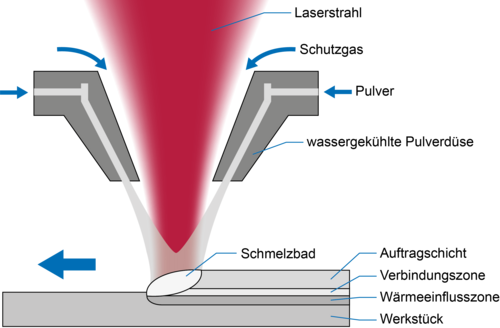
Grundlegende Funktionsweise
Bevor wir uns den Stärken des Laserauftragschweißens widmen, gehen wir erst mal einen Schritt zurück und schauen uns die grundlegende Funktionsweise näher an. Der Laser dient hier ganz einfach als Wärmequelle. Er schmilzt die Werkstückoberfläche auf, und in das Schmelzbad wird ein Beschichtungsmaterial eingebracht – entweder als Pulver oder Draht. Dieses wird mit aufgeschmolzen, sodass sich Oberflächen- und Beschichtungsmaterial vermischen. Nach dem Erkalten bleibt eine feste Schmelzverbindung zweier Metalle zurück, die auch als metallurgische Verbindung bezeichnet wird.
In der Art der Bindung zwischen Grund- und Beschichtungsmaterial liegt nun auch schon ein wesentlicher Vorteil des Laserauftragschweißens. Denn metallurgische Verbindungen sind sehr robust und besitzen eine lange Haltbarkeit. Zum Vergleich: Beim Thermischen Spritzen wird das Beschichtungsmaterial erhitzt und mit hoher Geschwindigkeit auf die Bauteiloberfläche geschleudert – mit dem Ergebnis, dass die Beschichtung lediglich durch eine mechanische Verklammerung haftet. Bei harten Stößen und Schlägen platzt sie leicht ab. Bessere Ergebnisse erzielen per Lichtbogenschweißverfahren aufgetragene Beschichtungen. Diese Verfahren nutzen zwar als Wärmequelle keinen Laser, sondern einen Lichtbogen, laufen im Prinzip aber ähnlich ab. Auch hier werden stabile, metallurgische Verbindungen von hoher Haltbarkeit erzeugt. Gleichzeitig ist die Wärmequelle selbst aber auch ein wesentlicher Nachteil. Denn der hohe Energieeintrag des Lichtbogens kann das Bauteil verformen, was anschließend ein aufwendiges Richten erfordert. Zudem lassen sich präzise, dünne Beschichtungen so kaum realisieren.
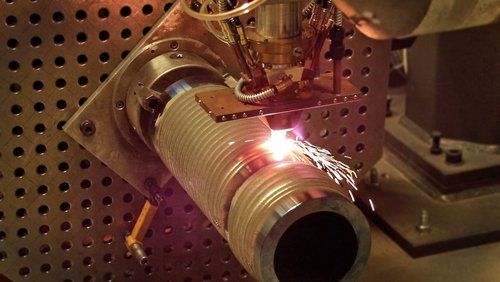
Top-Hat-Profil
Gerade hier kann hingegen das Laserauftragschweißen punkten. Für das Aufschmelzen reichen kurze, aber intensive Energieeinträge aus, die keine Verformung verursachen. Zudem kann der Energieeintrag auch bei laufendem Prozess feinabgestuft reguliert werden. Die Bestrahlung lässt sich also an jede Bauteilzone sehr genau anpassen, wovon insbesondere hochempfindliche, filigrane Bauteile profitieren. Die besten Ergebnisse beim Laserauftragschweißen werden in aller Regel mit Diodenlasern erzielt.
Das sogenannte Top-Hat-Profil des Lasers erzeugt gleichmäßige Energieeinträge und sorgt damit für eine einheitliche Oberflächenbehandlung. Dadurch kommt es zu einer geringen Aufmischung von Beschichtungs- und Grundmaterial, und es können besonders dünne Schichten realisiert werden. Bei anderen Lasertypen mit klassischem Gaußstrahl hingegen entsteht aufgrund der hohen Intensität in der Strahlmitte eine deutlich stärkere Aufmischung. Weitere Vorteile bietet der diodenlasertypische Wellenlängenmix. Er erzeugt sehr ruhige und spritzerarme Schmelzbäder und stellt damit hohe Beschichtungsqualitäten sicher. Und obendrein gibt auch die Wirtschaftlichkeit des Diodenlaser keinen Anlass zu Kritik. Mit einem Wirkungsgrad bis zu 50 Prozent besitzt er die höchste Energieeffizienz aller verfügbaren Industrielaser.
Fazit
Im Endeffekt lassen sich mit dem diodenlaserbasierten Laserauftragschweißen je nach Präferenz durchschnittliche bis sehr dünne Schichten erzielen, die durch ihre hohe Stabilität auch harten Schlägen und Stößen widerstehen. Abhängig von Motivation und Beschichtungsmaterial können solche Beschichtungen Bauteiloberflächen vor Verschleiß und Korrosion schützen und Standzeiten somit deutlich erhöhen. Neben Erstbeschichtungen wird das Verfahren auch erfolgreich zur Reparatur von abgenutzten Oberflächen oder beschädigten Bauteilen eingesetzt. Ein weiterer wichtiger Anwendungsbereich des Laserauftragschweißens ist die Additive Fertigung, auch bekannt als 3D-Druck. Hier werden Schichten aus identischen oder unterschiedlichen Materialien aufgebracht, die Lage um Lage ganze Bauteile in nahezu jeder gewünschten Form oder Struktur ergeben.
Schon dieser kurze Überblick zeigt: Das diodenlaserbasierte Laserauftragschweißen eröffnet eine Vielzahl von Bearbeitungsmöglichkeiten und kann durch hohe Qualitätsstandards überzeugen, die viele andere Verfahren nicht immer erfüllen. Doch wie genau sehen die drei Hauptanwendungen – Beschichten, Reparieren und Generieren – nun im Einzelnen aus? Und wo werden sie eingesetzt? Antworten auf diese Fragen gibt es in den kommenden drei Teilen unserer Serie.
Erfahren Sie mehr über das Laser Cladding.