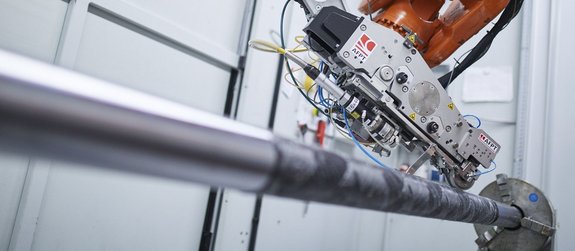
Direktdiodenlaser optimieren Tapelegen faserverstärkter Kunststoffe
Beim Herstellen von Leichtbaukomponenten durch laserbasiertes Tapelegen und –wickeln wurden in der Vergangenheit bereits beachtliche Ablegegeschwindigkeiten erreicht. Die herkömmlichen Anlagen mit nur einem einzigen Bearbeitungskopf besaßen jedoch nur eingeschränkte Produktionskapazitäten. Laserline Direktdiodenlaser machen nun Fertigungsanlagen mit mehreren Bearbeitungsköpfen und dadurch eine deutliche Kapazitätssteigerung möglich.
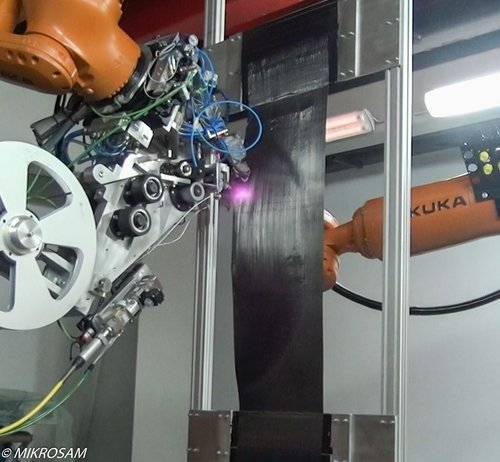
Nachfrage nach Leichtbaukomponenten
Die Nachfrage nach Leichtbaukomponenten nimmt heute in vielen Konstruktionsbereichen zu. Im Automobilbau, in der Luft- und Raumfahrttechnik, aber auch im Pipelinebau weiß man die Gewichtsvorteile gegenüber dem klassischen Werkstoff Stahl zu schätzen. Neben dem Leichtmetall Aluminium kommen dabei vor allem faserverstärkte Kunststoffe zum Einsatz. Sie sind noch einmal um 25 Prozent leichter als Aluminium und um 60 bis 70 Prozent leichter als Stahl. Das typische Verfahren zur Herstellung solcher Kunststoffbauteile ist dabei die Verarbeitung in Form von Tapes. Hierfür gibt es unterschiedliche Ansätze: Im sogenannten Duroplast-Tapelegeverfahren etwa werden die Tapes mittels eines Klebers verbunden. Durch unidirektionales Ablegen der vorimprägnierten Fasern und die anschließende Konsolidierung in einem Druckbehälter (Autoklavierprozess) entstehen schließlich die fertigen Bauteile. Nachteil dieses Ansatzes: Eine spätere Aufwärmung oder Umformung ist nicht möglich, und der Kleber gilt als gesundheitsschädlich. Zudem ist das Material nicht recycelbar.
Industriell erfolgreicher war bisher ein zweiter Ansatz, der auf der Verwendung thermoplastischer Matrixsysteme basiert. Diese werden ebenfalls als Tapes verarbeitet, beim Legen oder Wickeln aber sofort konsolidiert. Wie ist hier das Vorgehen? Beim Tapelegen werden die Tapes mithilfe einer Vorschubeinheit von der Rolle abgezogen, auf der Arbeitsplattform oder dem Bauteil abgelegt und durch Aufschmelzen kurz vor der Konsolidierungszone stoffschlüssig miteinander verbunden. So entstehen beispielsweise Organobleche oder lokale Verstärkungen großflächiger Kunststoffbauteile. Zur Herstellung von Rohren, Wellen oder Tanks werden die Tapes mittels einer Art Kreuzwicklung auf einem rotierenden Behälter oder Rohr abgelegt und während des Prozesses direkt konsolidiert. Zum Aufschmelzen dient bei beiden Verfahren eine Hochleistungswärmequelle, zur Fixierung eine Druckrolle. Mögliche Wärmequellen sind Infrarot- oder Halogen-Strahler, Heißgas oder Laser. Die Zukunft gehört jedoch zweifellos dem lasergestützten Thermoplast-Tapelegeverfahren: Es verbindet einen kurzen, lokal konzentrierten und temperaturgeregelten Wärmeeintrag in die Bandmatrix mit einem hohen Automatisierungsgrad und bietet dadurch das größte wirtschaftliche Potenzial.
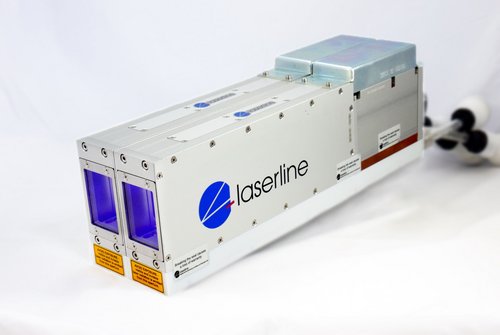
Direktdiodenlaser mit mehreren Bearbeitungsköpfen für die Serienfertigung
In der Serienfertigung wird das laserbasierte Tapelegeverfahren denn auch schon seit 2009 eingesetzt. Da die herkömmlichen Fertigungsanlagen bislang nur über einen einzigen Bearbeitungskopf verfügten, waren den Produktionskapazitäten allerdings spürbare Grenzen gesetzt. Durch eine Neuentwicklung von Laserline zeichnet sich hier jedoch ein Ausweg ab: Mit dem LDMdirect steht Anwendern ab sofort ein modularer Direktdiodenlaser im 19-Zoll-Design zur Verfügung, mit maximal 2 kW Ausgangsleistung und einer Gehäusebreite des Laserkopfes von unter 50 mm. Diese kompakte Bauweise erleichtert den Einbau in Roboter oder Maschinen und ermöglicht es insbesondere, mehrere Bearbeitungsköpfe in eine Aufspannung nebeneinander zu integrieren und so zur Parallelbearbeitung handelsüblicher Tapebreiten zu nutzen. Prozessgeschwindigkeit und Produktionskapazität erhöhen sich dadurch erheblich. Damit sind endlich auch die Voraussetzungen für eine wirtschaftliche Großserienfertigung im Bereich des Tapelegens geschaffen.
Wie aber steht es um die Bearbeitung von Endlos-Rohren für Pipelines oder Wasserleitungen? Für diesen Anwendungsfall entwickelte Laserline einen weltweit einzigartigen rotierenden Multi-kW-Diodenlaser für Endloswickelmaschinen. Das Verfahren: Mehrere Laser rotieren zeitgleich auf einer Drehvorrichtung um die Längsachse des Rohres, jeder Laser verschweißt ein Tape, während das Rohr dabei vor- und zurückbewegt wird. Der Prozess wird fortgesetzt, bis die notwendige Anzahl an Lagen erreicht ist.
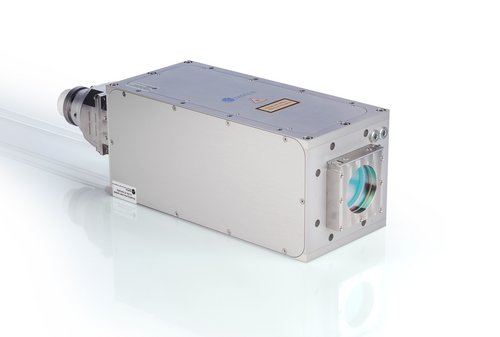
Zoomfunktion für eine Anpassung des Laserstrahls
Auch im Bereich der Bearbeitungsoptiken ging Laserline neue Wege und entwickelte Homogenisierungsoptiken mit Zoomfunktion, die gezielt auf die besonderen Anforderungen der Tapeverarbeitung ausgelegt wurden. Spezielle optische Linsen erzeugen hier einen variablen, rechteckigen Laserstrahl, der problemlos auf die Tapebreite abgestimmt werden kann. Die Homogenisierungsoptiken optimieren die ohnehin sehr gleichmäßige Intensitätsverteilung des Lasers noch einmal zusätzlich und ermöglichen zudem eine Anpassung des Laserstrahls an die Legegeschwindigkeit der Tapes. Die Bestrahlungsparameter können je nach Bedarf über den gesamten Prozess beibehalten oder zwischendurch angepasst werden.
Neue Möglichkeiten
Die Neuentwicklungen im Bereich der Diodenlasertechnologie haben der Tapelegeverarbeitung also insgesamt sowohl technisch als auch wirtschaftlich neue Möglichkeiten erschlossen. Hierzu tragen nicht zuletzt auch die typischen Pluspunkte bei, die der LDMdirect mit allen anderen Laserline Diodenlasern teilt: Durch eine feinabgestufte Leistungssteuerung im Millisekundentakt lässt sich der Temperatureintrag präzise regulieren, sodass es beim Aufschmelzen der Tapes nicht zu einer Zersetzung der Kunststoffmatrix kommen kann. Die Ausgangsleistung ist stabil, und durch den geringen Verschleiß der Systemkomponenten ergeben sich kaum Wartungskosten. Mit einem Wirkungsgradwert von über 50 Prozent besitzen die Laserline Diodenlaser zudem die höchste Energieeffizienz im Industrielaserumfeld. Die Nachhaltigkeit dieses Verfahrens wird noch gesteigert durch die Möglichkeit, das Material vollständig zu recyceln. All das zusammen hält die Gesamtbetriebskosten niedrig und macht den Weg frei für lohnende Großproduktionen im Bereich von Kunststoff-Leichtbaukomponenten – seien es nun Pipelinerohre, Autotüren oder Flugzeugtragflächen.
Erfahren Sie mehr zum automatisierten Tapelegen mit Diodenlasern!