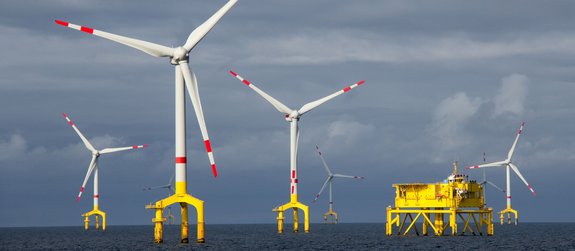
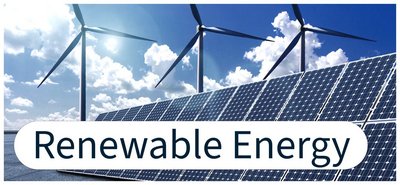
Beschichtung von Windkraftanlagen-Gleitlagern
Die diodenlaserbasierte Beschichtung von Windkraftanlagen-Gleitlagern wird immer beliebter. Hauptgrund dafür ist neben der Wirtschaftlichkeit des Verfahrens und der herausragenden Qualität der Beschichtungen, dass dieser Prozess ohne gesundheitsschädliche bleihaltige Kupfer-Zinn-Legierungen auskommt.
Diodenlaserbasiertes Cladding erhöht Standzeiten und erlaubt Steigerung der Prozessgeschwindigkeiten
Die Bundesregierung hat mit der Verabschiedung der EEG-Novelle die Ausbauziele für Windkraftanlagen (WKA) erhöht: An Land ist eine Steigerung auf 115 Gigawatt (GW) bis zum Jahr 2030 das erklärte Ziel; im Offshore-Bereich sind Leistungen von 30 GW bis 2030 bzw. 70 GW bis 2045 vorgesehen. Dieser flächendeckende Ausbau der Windenergie wird entscheidend zur Energiewende beitragen. Daher ist es umso wichtiger, dass Schlüsselkomponenten wie Gleitlager nicht nur qualitativ hochwertig und langlebig sind, sondern auch energie- und ressourcenschonend hergestellt werden. Hier übernimmt die Beschichtung von Gleitlagern eine Schlüsselrolle: Sie reduziert Reibungswiderstände und erhöht so die Standzeiten der Komponenten. Bislang wurden WKA-Gleitlager zumeist im Schleudergussverfahren oder im Ofen beschichtet. Allerdings haben diese Prozesse auch einige Schwächen: Die häufig erdgasbasierten Verfahren sind nicht nur energieintensiv, es ist auch ein erheblicher Materialeinsatz notwendig, um qualitativ hochwertige Ergebnisse zu erzielen. Indes erweist sich das Laserauftraglöten bzw. Laser Deposition Brazing als Alternative: Es überzeugt nicht nur mit einem niedrigeren Energie- und Materialverbrauch, sondern auch durch dünnere und dennoch widerstandsfähige, gut definierte und bleifreie Beschichtungen von höchster Qualität.
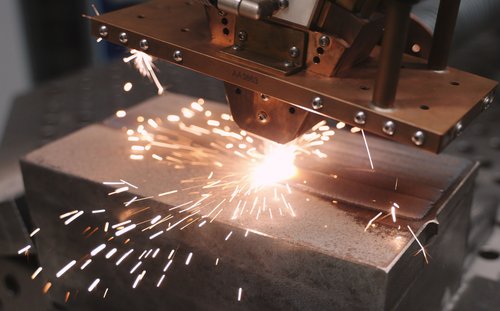
High Power-Auftragschweißen mit Diodenlaser
Möglich werden diese Resultate durch den Einsatz von Hochleistungsverfahren, die den Wärmeeintrag in das Werkstück auf ein Minimum beschränken. Bei WKA-Gleitlagern werden für die Beschichtung des Außendurchmessers – also des Schaftes – üblicherweise Buntmetalle und Kupfer-Zinn-Legierungen eingesetzt, die in einem einstufigen Prozess mit Prozessgeschwindigkeiten von mehreren Metern pro Minute aufgetragen werden. So entsteht eine strapazierfähige und robuste Verbindung zwischen Grund- und Beschichtungswerkstoff. Ein zentraler Vorteil des Laser Claddings ist dabei seine Flexibilität, die es beispielsweise erlaubt, Spotgröße und -geometrie sowie die Laserleistung den Kundenwünschen anzupassen.
Die Qual der Wahl: Draht oder Pulver
Entscheidenden Einfluss auf die genauen Prozessparameter hat jedoch nicht zuletzt auch die Wahl des Beschichtungsmaterials – Pulver oder Draht. Beim drahtbasierten Laserauftraglöten liegen die Auftragsraten typischerweise bei 0,5 kg/h pro kW Laserleistung. Zudem bietet Laserline neben verschiedenen Mehrdraht- und Heißdrahtapplikationen auch anwendungsspezifische kundenindividuelle Lösungen an. Ein großer Pluspunkt der drahtbasierten Methode ist, dass kein Abfallmaterial entsteht. Allerdings ist das Materialsortiment begrenzt, was die Individualisierungsmöglichkeiten einschränkt.
Das pulverbasierte Laserauftraglöten hingegen punktet mit einem breiten Sortiment. Und ein Pulverwirkungsgrad von bis zu 95 Prozent garantiert, dass es auch hier kaum zu Materialverlusten kommt. Der Laserstrahl schmilzt zudem das Pulver besonders gleichmäßig auf, wodurch ein sehr ruhiges Schmelzbad entsteht. Als überaus vorteilhaft haben sich dabei Breitstrahldüsen erwiesen, da sie eine besonders schnelle Beschichtung bzw. einen höheren Materialauftrag in derselben Zeit ermöglichen. Die Auftragsrate liegt in diesem Fall bei 133 g/min (bzw. 8 kg/h), sodass sich Schichten von circa 1,4 mm Dicke mit einer Geschwindigkeit von 100 bis 200 cm2/min aufbauen lassen. Aber auch der Einsatz eines Rundspots mit einem Durchmesser von 6 bis 12,5 mm und einer Leistung von 5 kW ist möglich. Die Auftragsrate liegt hier bei 45 g/min (2,7 kg/h), sodass sich bei einer Prozessgeschwindigkeit von 1,5 m/min Schichtdicken von circa 1 mm realisieren lassen. Ferner besteht auch die Option, den Gleitlagerinnendurchmesser zu beschichten. Laserline bietet auch hier verschiedene Lösungen an.
High-Speed-Beschichtung
Damit ist in Sachen Entwicklung das Ende der Fahnenstange allerdings noch nicht erreicht. Vielmehr wird kontinuierlich an einer weiteren Steigerung der Prozessgeschwindigkeiten gearbeitet: Aktuell lassen sich bereits Auftragsraten von über 10 kg/h bei Prozessgeschwindigkeiten von bis zu 200 m/min realisieren, was einer Flächenauftragsrate von bis zu 10 m2/h entspricht. Möglich werden diese hohen Bearbeitungsgeschwindigkeiten durch eine Steigerung der Laserleistung auf über 20 kW. Gleichzeitig unterstützt das diodenlaserbasierte Auftraglöten aber auch den Aufbau besonders dünner Schichten mit Dicken ab 0,2 mm, die dennoch hochstabil sind. (Gründe dafür sind, dass es während der Laserbeschichtung kaum zu Porenbildung kommt und eine robuste schmelzmetallurgische Verbindung zwischen Komponenten und Beschichtungswerkstoff entsteht.) Da der Pulverwirkungsgrad beim High Speed Laser Deposition Brazing bei bis zu 90 Prozent liegt und der Materialeinsatz zugleich aufgrund der geringen Schichtdicken niedriger ist als beim klassischen Laser Cladding, stellt dieser Ansatz eine überaus nachhaltige Option dar.
Verbessertes Prozess- und Komponentenmonitoring
Bereits diese kurze Ausführung macht deutlich, dass die diodenlaserbasierte Beschichtung viele Vorteile bietet: Der geringere Energieverbrauch und die Materialeinsparungen machen die Herstellung von WKA-Gleitlagern deutlich nachhaltiger; durch den Verzicht auf bleihaltige Substanzen ist das Verfahren gesundheitsverträglicher und umweltfreundlicher. Weiterer Pluspunkt: Der geringere Nachbearbeitungsbedarf beschleunigt die Produktion erheblich.
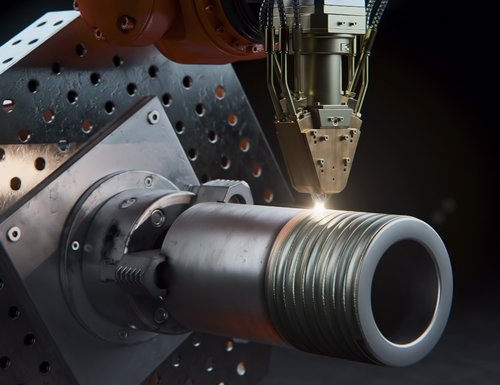
Der Prozess ist mittlerweile hinlänglich erprobt und wird auch bereits in der Serienfertigung eingesetzt. Neue, umfassende Methoden der Prozess- und Komponentenüberwachung ermöglichen nun zudem eine zuverlässigere Fehlererkennung und Qualitätskontrolle. Mit Hilfe von softwaregestützten Infrarotkameras sowie Systemen zur Messung von Prozessemissionen lässt sich etwa das Auftreten von Poren und anderen Materialfehlern weitestgehend unterbinden. Kommt es bei der Beschichtung doch einmal zu Unregelmäßigkeiten, registrieren die Systeme diese, und die betreffende Komponente kann im Nachgang gezielt ausgesteuert werden. Auch die spätere Fehleranalyse wird durch ein koaxiales Monitoring der Prozessemissionen erleichtert. Die gesammelten Daten lassen sich allerdings nicht nur zur Qualitätskontrolle einsetzen. Vielmehr sollen sie perspektivisch auch für Industrie 4.0- und Smart-Factory-Anwendungen nutzbar gemacht werden.